Material Analysis
Non-Destructive and Destructive Testing
Praesent ac adipiscing ullamcorper semper ut amet ac risus. Lorem sapien ut odio odio nunc. Ac adipiscing nibh porttitor erat risus justo adipiscing adipiscing amet placerat accumsan. Vis. Faucibus odio magna tempus adipiscing a non. In mi primis arcu ut non accumsan vivamus ac blandit adipiscing adipiscing arcu metus praesent turpis eu ac lacinia nunc ac commodo gravida adipiscing eget accumsan ac nunc adipiscing adipiscing.
Visual and Optical Testing (VT)
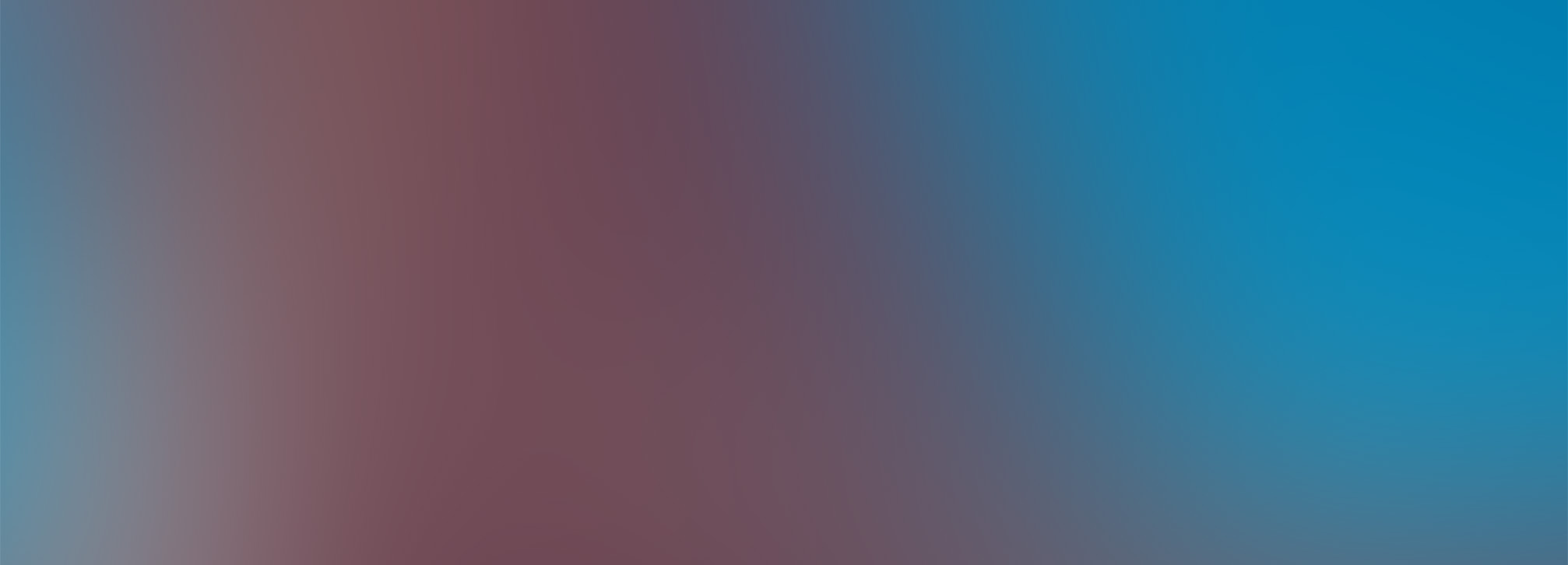
The most basic NDT method is visual examination. Visual examiners follow procedures that range from simply looking at a part to see if surface imperfections are visible, to using computer controlled camera systems to automatically recognize and measure features of a component.
Radiography (RT)
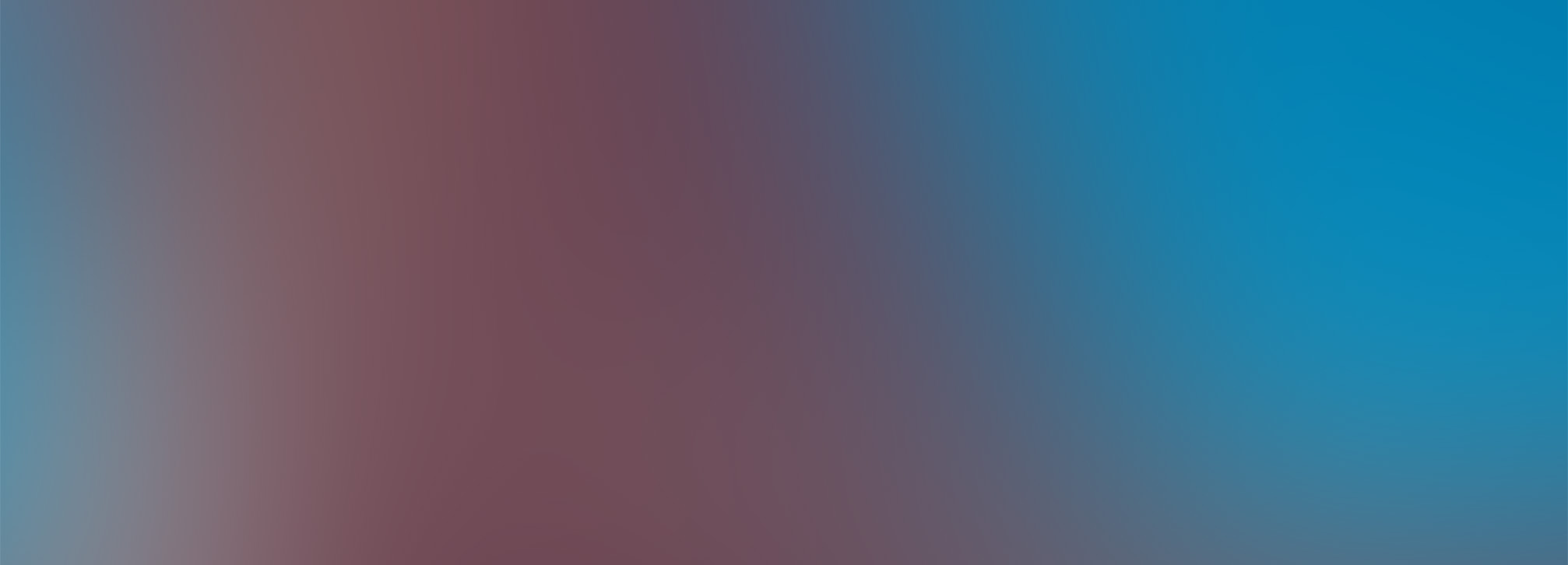
RT involves using penetrating gamma- or X-radiation on materials and products to look for defects or examine internal or hidden features. An X-ray generator or radioactive isotope is used as the source of radiation. Radiation is directed through a part and onto film or other detector. The resulting shadowgraph shows the internal features and soundness of the part. Material thickness and density changes are indicated as lighter or darker areas on the film or detector. The darker areas in the radiograph below represent internal voids in the component.
Hydrostatic Testing (HT)
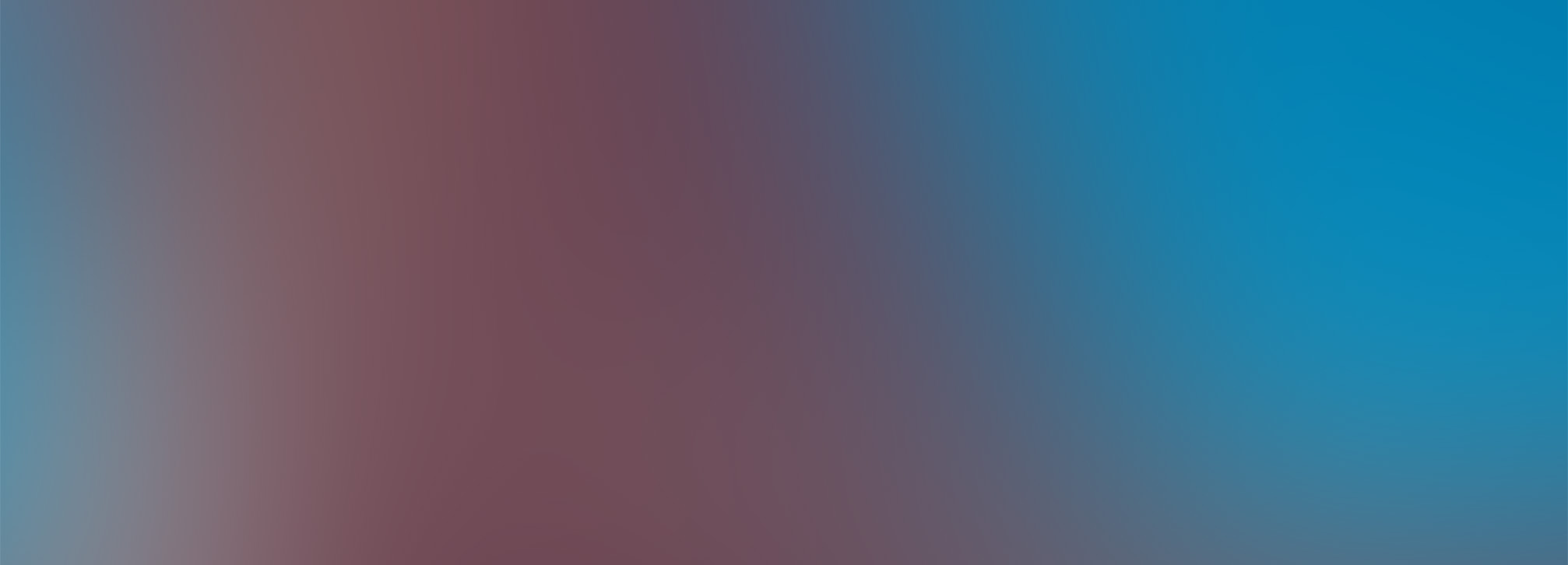
Nunc lacinia ante nunc ac lobortis. Interdum adipiscing gravida odio porttitor sem non mi integer non faucibus ornare mi ut ante amet placerat aliquet. Volutpat commodo eu sed ante lacinia. Sapien a lorem in integer ornare praesent commodo adipiscing arcu in massa commodo lorem accumsan at odio massa ac ac. Semper adipiscing varius montes viverra nibh in adipiscing blandit tempus accumsan.
Electromagnetic Testing (ET)
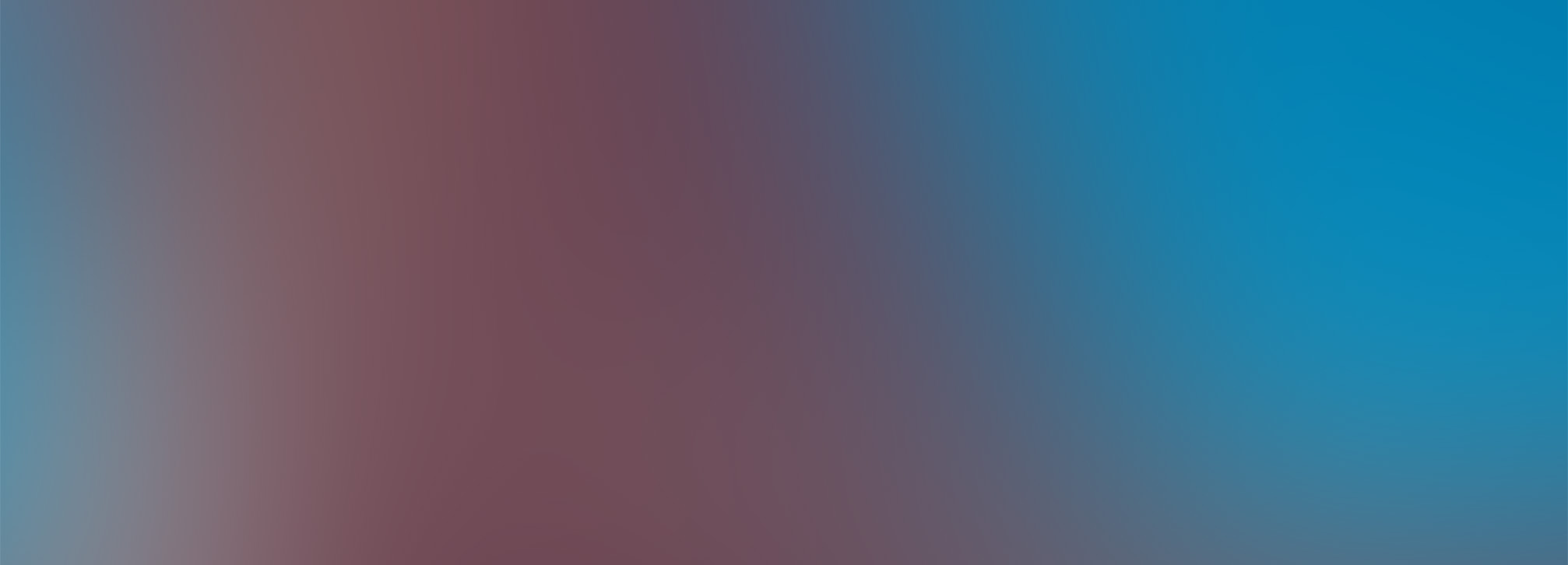
There are a number of electromagnetic testing methods but the focus here will be on eddy current testing. In eddy current testing, electrical currents (eddy currents) are generated in a conductive material by a changing magnetic field. The strength of these eddy currents can be measured. Material defects cause interruptions in the flow of the eddy currents which alert the inspector to the presence of a defect or other change in the material. Eddy currents are also affected by the electrical conductivity and magnetic permeability of a material, which makes it possible to sort some materials based on these properties. The technician in the image is inspecting an aircraft wing for defects.
Magnetic Particle Testing (MT)
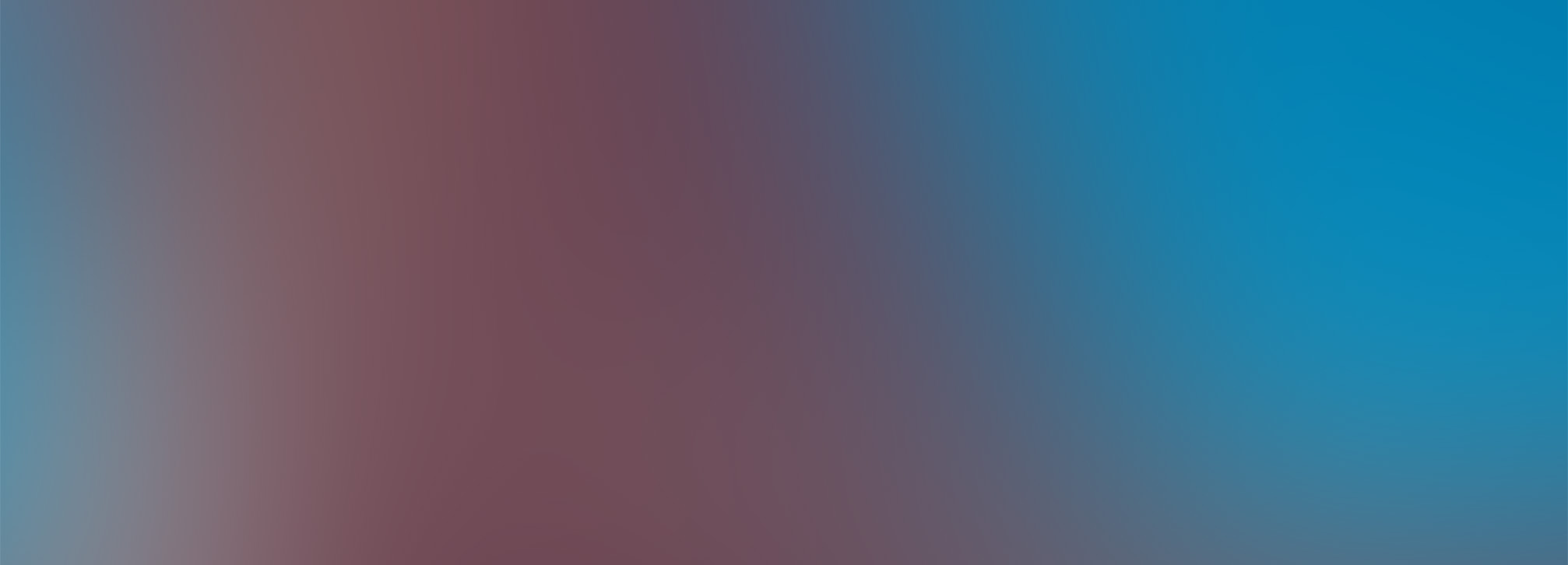
This NDT method is accomplished by inducing a magnetic field in a ferromagnetic material and then dusting the surface with iron particles (either dry or suspended in liquid). Surface and near-surface flaws disrupt the flow of the magnetic field within the part and force some of the field to leak out at the surface. Iron particles are attracted and concentrated at sites of the magnetic flux leakages. This produces a visible indication of defect on the surface of the material. The images above demonstrate a component before and after inspection using dry magnetic particles.
Ultrasonic Testing (UT)
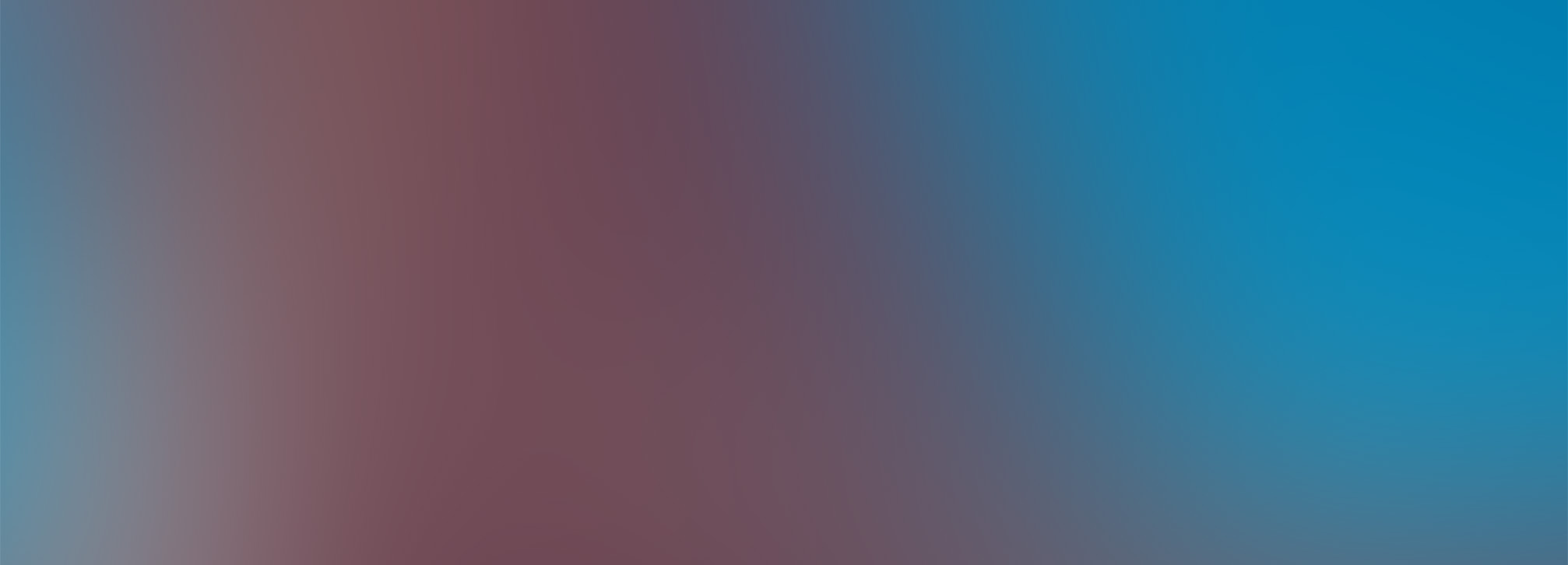
In ultrasonic testing, high-frequency sound waves are transmitted into a material to detect imperfections or to locate changes in material properties. The most commonly used ultrasonic testing technique is pulse echo, whereby sound is introduced into a test object and reflections (echoes) from internal imperfections or the part's geometrical surfaces are returned to a receiver. Below is an example of shear wave weld inspection. Notice the indication extending to the upper limits of the screen. This indication is produced by sound reflected from a defect within the weld.
Penetrant Testing (PT)
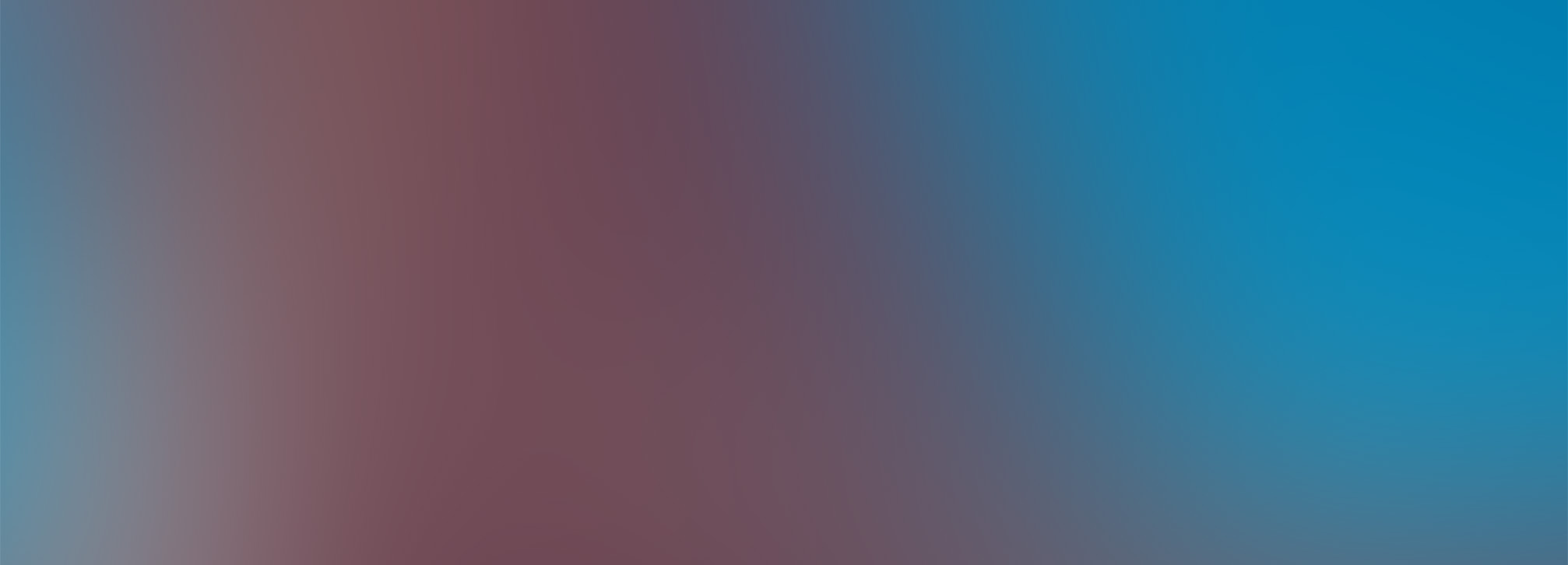
With this testing method, the test object is coated with a solution that contains a visible or fluorescent dye. Excess solution is then removed from the surface of the object but is left in surface breaking defects. A developer is then applied to draw the penetrant out of the defects. With fluorescent dyes, ultraviolet light is used to make the bleedout fluoresce brightly, thus allowing imperfections to be readily seen. With visible dyes, a vivid color contrast between the penetrant and developer makes the bleedout easy to see. The red indications in the image represent a defect in this component.